Plasmatron
Focussed on your success
Plasmatron is an arc welding process in which, similar to the TIG process, an arc is ignited between a tungsten electrode and the workpiece.
By focussing the arc using special nozzle geometries, higher welding speeds and lower distortion can be achieved.
Plasmatron is a splatter-free welding process and usually used for high-quality visible seams. In the case of stainless steel applications, temper colours are prevented via the use of additional gas shielding.
Efficiency
To achieve high system availabilities, great importance was attached to being able to replace wear parts quickly. Manual replacement within a few seconds or fully automated replacement in-line during component transport ensures the maximum productivity of your plant.
Plasmatron is used for thin stainless steel sheets, for brazing galvanised sheet metal and for welding aluminium components.
Plasmatron highlights:
Visual appearance:
Plasmatron is a splatter-free welding process and usually used for high-quality visible seams. In the case of stainless steel applications, temper colours are prevented via the use of additional gas shielding.
Welding speed:
Since the arc in the Plasmatron process is highly focussed, we achieve a large increase in energy density. This in turn leads to higher speeds, which significantly reduces the energy input into the component concerned.
Low distortion
Due to the focussed arc and the targeted heat input into the component, the distortion in the component can be minimised.
Automation capability
Our objective is to produce highly automated machine using the Plasmatron welding process. The torch was therefore designed so that the cathode can be replaced automatically during operation without the need for a worker to intervene.
This is achieved by an automatic cathode changing system.
Plasmatron summary
Advantages in comparison to laser welding
Advantages in comparison to MAG welding
Advantages in comparison to TIG welding
Additional welding processes
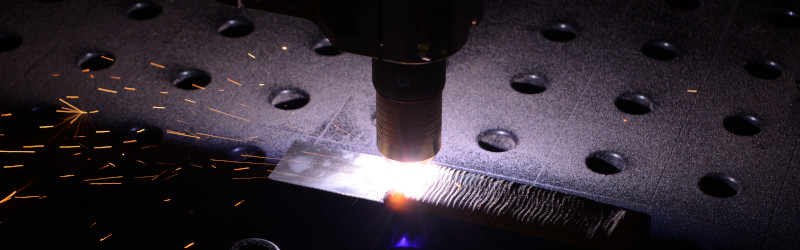
Plasma
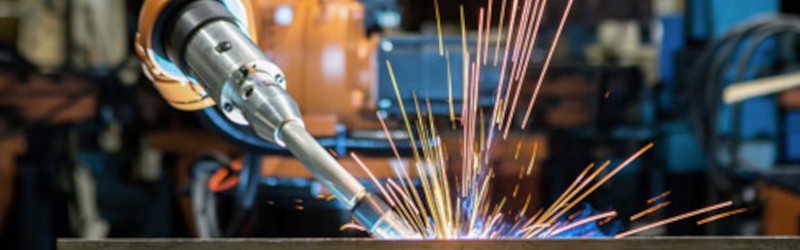
MIG / MAG
To the products
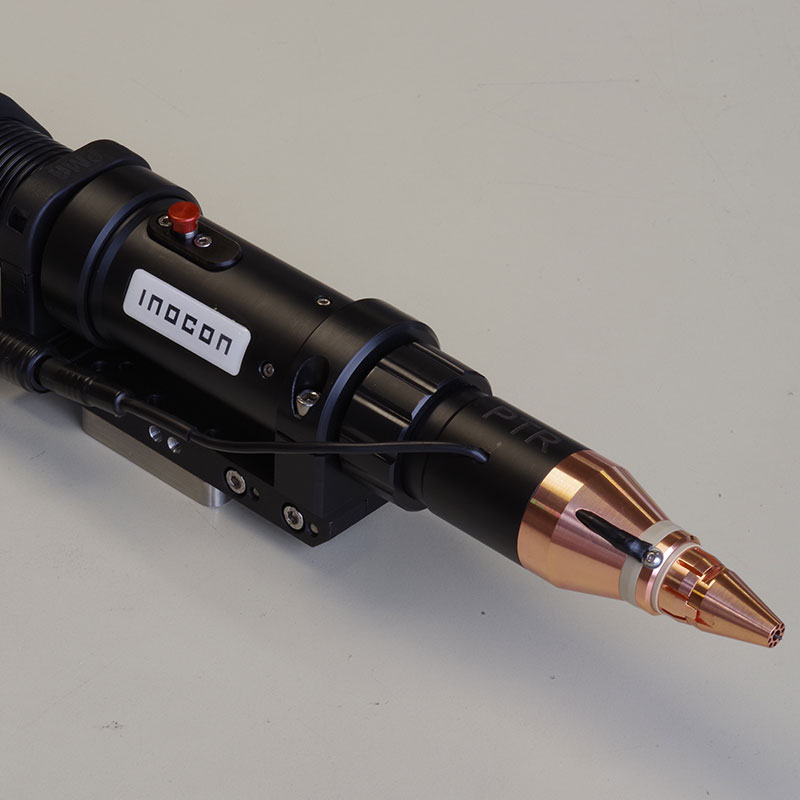
Plasmatron torch
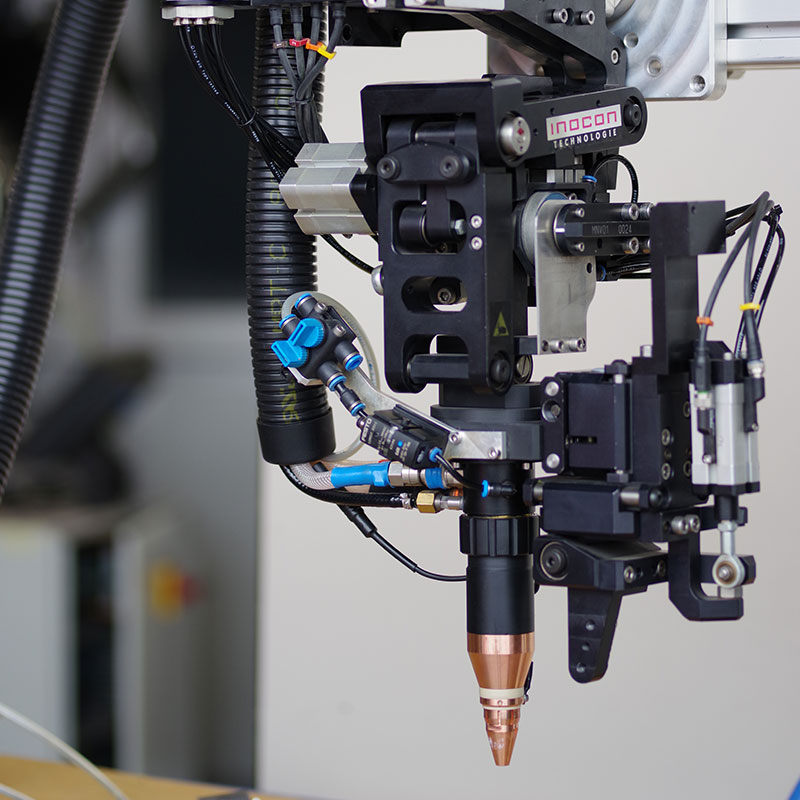
Seam guidance
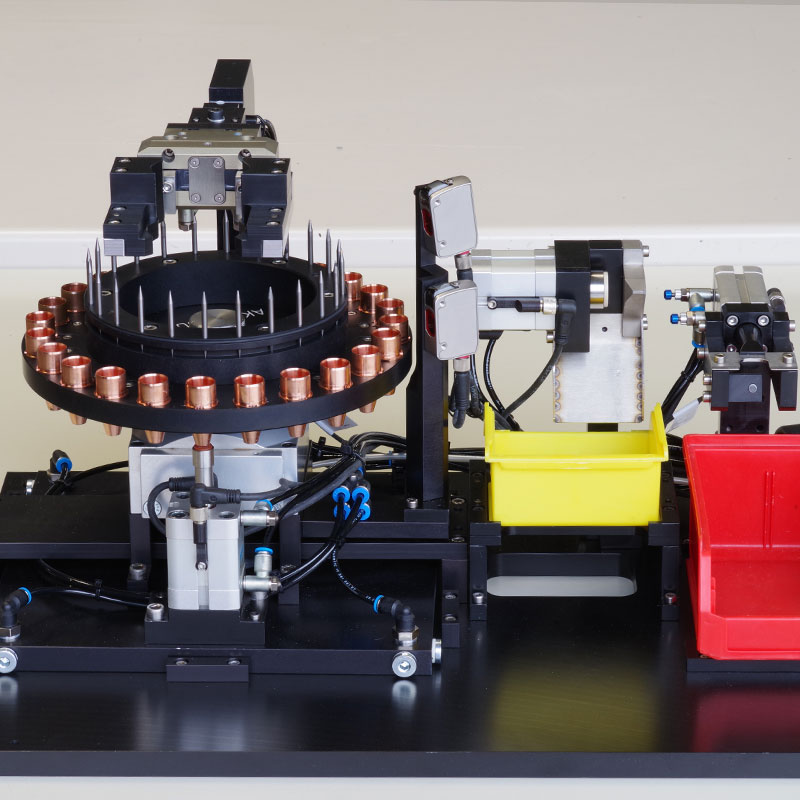
Cathode changer
To the projects
If this appeals to you, send us your application and become part of our team.